Our Technologies
At Instant 3D, we believe that in 2024, manufacturing must also move into the future. That’s why we’ve brought together and made our manufacturing capabilities available under a single roof.
Time to end the problems caused by uncertainty and delays from your manufacturing partners! Request a proposal from us and you can be sure that your manufacturing projects are in good hands.
3D printing
Our industrial 3D printing machines build objects from thin layers based on computer models. This innovative manufacturing technology has virtually no geometric limits, and can produce any shape and form imaginable, even geometries where traditional technologies fail.
We use ABS plastic and high-quality photopolymers for printing, which are ideal for durable and resistant parts.
We constantly monitor the service prices in the rapid prototyping sector to ensure that we offer the most competitive prices. In most cases we work 20-50% below market prices.
- Upload your 3D plans
- Choose your technology and raw material
- Get a quote within 48 hours and order production.
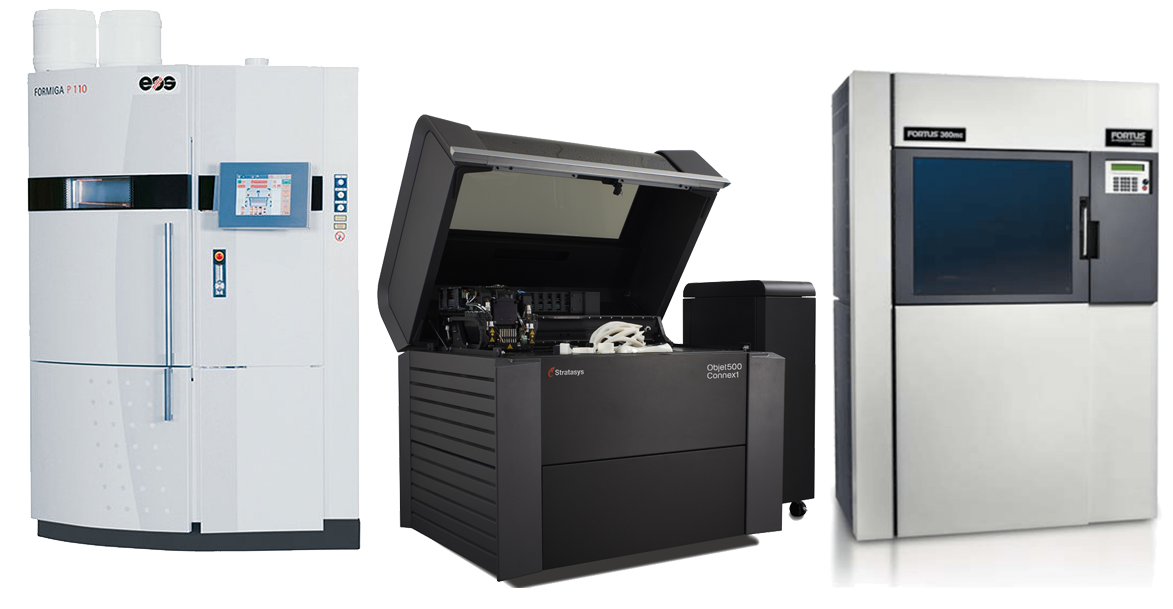
Quality parts, quickly and accurately




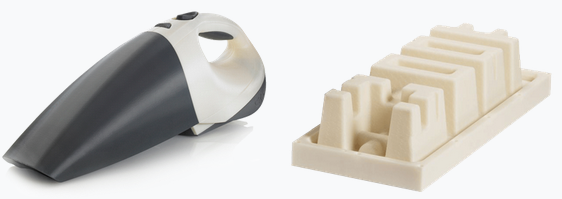
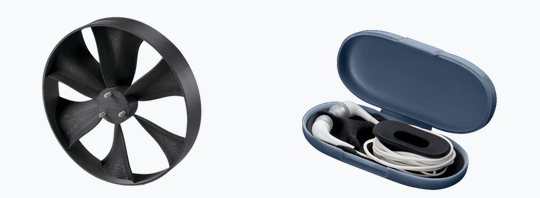

Production time | 2-7 working days |
Technologies | Polyjet, Industrial FDM, SLS, DLP |
Raw Material | Thermoplastics, photopolymer resins |
Effective piece count | Individual pieces, small series |
Max object size | 100+ cm |
CNC milling
CNC milling is a so-called subtractive, or material separation, manufacturing technology. It is entirely computer-controlled, where the material is gradually removed from an initial block of material or sheet by a high-speed rotating milling head. From these negative spaces, the final geometry of the manufactured part is formed.
The advantage of the technology is that it can be used to machine a wide range of materials, metals and plastics, and that it can be done with high production quality and precision. Disadvantages include the relative high skill requirements and limited productivity.
- Upload your 3D plans
- Choose your technology and raw material
- Get a quote within 48 hours and then order production.
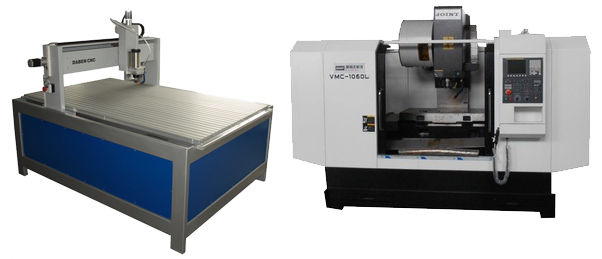
Precision milling, from experts




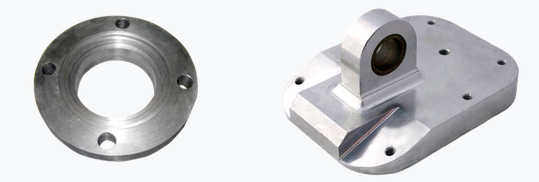

Production time | 2-15 working days |
Raw material | Wood, plastics , aluminium |
Optimal series size | Low/Medium |
Max object size | 100+ cm |
Injection moulding
njection moulding is a mass production manufacturing technology that enables the production of complex shaped products.
The injection moulding process involves the injection of a molten plastic material into a pre-made metal mould at high pressure and temperature. The cavities of the metal mould produce the exact geometry of the required part, which is then cooled in the mould at lightning speed to create the required part. The metal mould rims are then opened and the product is manually or automatically removed from the mould.
Injection moulding has the advantage that, with a properly automated process, it can produce hundreds or even thousands of products per hour, making it highly productive. The disadvantage is that it requires a mould to start production, which is a slow and expensive process requiring special skills.
- Upload your 3D plans
- Choose your technology and raw material
- Get a quote within 48 hours and then order production.
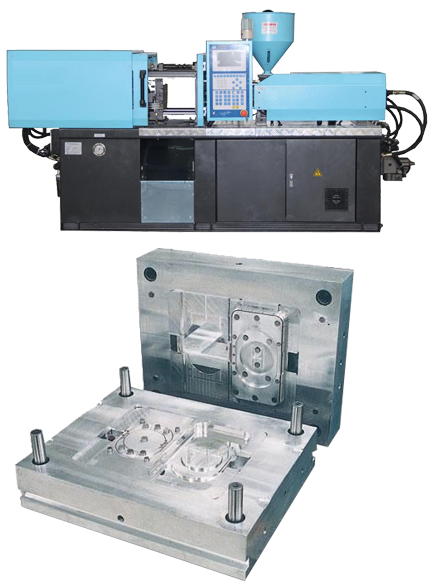
High volume production, under one roof




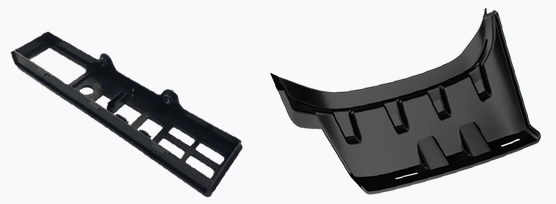
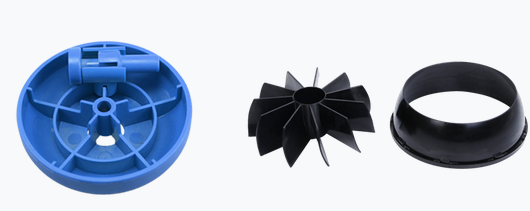

Production time | 30-90 working days |
Raw material | Thermoplastics |
Optimal series size | High |
Max object size | 50+ cm |
Sheet metal cutting
In our work we often work with parts that can be produced from flat sheets and plates, using laser cutting or flattening. The advantage of these processes is that even large parts can be produced at high speed using computer-controlled cutting machines, and the dimensional accuracy achieved can be within a few hundredths of a millimetre.
- Upload your 3D plans
- Choose your technology and raw material
- Get a quote within 48 hours and then order production.
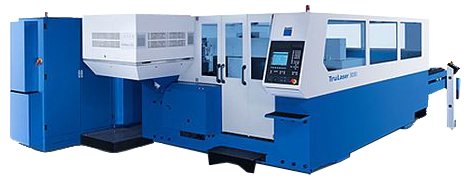
Disc parts quickly and accurately




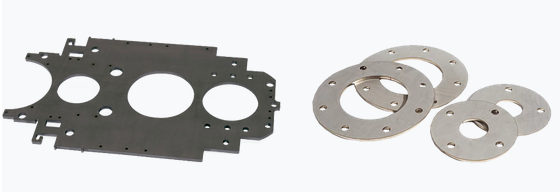
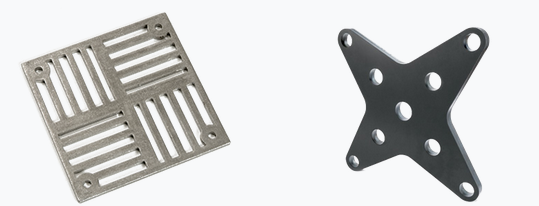

Production time | 3-15 working days |
Raw material | Carbon steel, stainless steel, aluminium |
Optimal series size | Medium/High |
Max object size | 100+ cm |
Sand moulding
Sand moulding is a foundry process where a casting pattern is pressed into a sand mixture to form a mould into which molten metal is then poured. This process works particularly well for small series size production. With automated equipment, the process can also be suitable for larger series sizes. The process of making sand moulds and cast metal parts is a relatively simple one, many parts of which can be automated, reducing cycle times and the amount of labour required.
However, making the mould itself is often a complicated, time-consuming and costly process. The most common way of making a pattern is CNC milling from aluminium. The main disadvantages of this are typically long delivery times and high costs.
Moreover, possible on-the-fly modifications, such as inadequate shrinkage compensation or possible design errors, require sample re-production, which entails additional high costs and delays.
Because of the problems of traditional prototyping, 3D printing has long been a technology used in foundry. It can save significant costs and labour, and ultimately help bring a product to market faster.
3D printed master objects are ideal if the casting is for prototyping or mass production, the casting geometry requires additional control, or the design of the casting channels requires refinement or if the geometry to be cast is large or complex.
The advantages of 3D printed master objects include the ability to produce the object at 40-70% lower cost, significantly shorter delivery times, faster design refinement and the ability to modify the moulding points and cuts afterwards.
- Upload your 3D plans
- Choose your technology and raw material
- Get a quote within 48 hours and then order production.
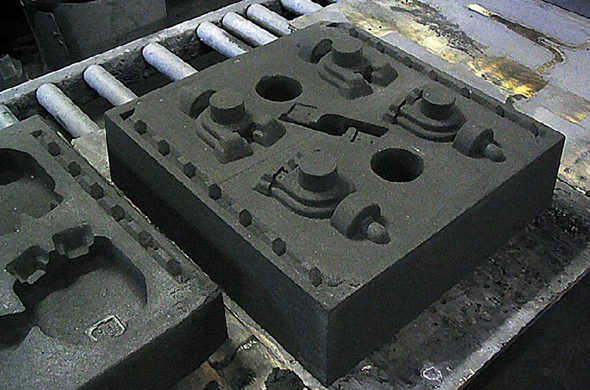
Sample preparation and sand moulding in one place




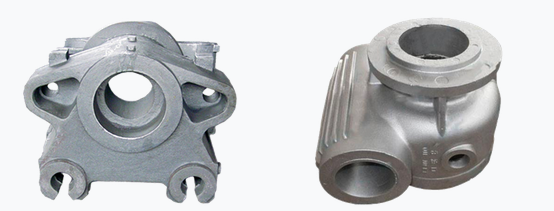
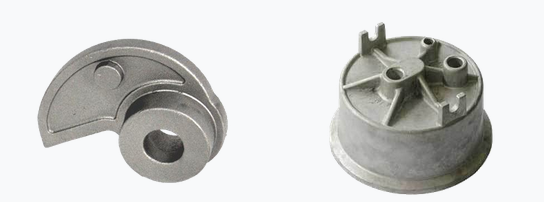

Production time | 7-20 working days |
Raw material | Aluminium, copper, bronze, iron |
Optimal series size | Low |
Max object size | 100+ cm |
Instant3D is a smart manufacturing platform where we’ve brought all our different manufacturing technologies under one roof, so you can access our full manufacturing capabilities with a single click: our advanced industrial 3D printers, CNC milling machines, laser cutters, and even our mass production and metal casting capabilities. Simply upload/send your 3D files and request for a price proposal. If you get stuck, our colleagues will be happy to help!
© 2020-2024 i3D Technologies Kft.
1117 Budapest, Hunyadi János út 3.
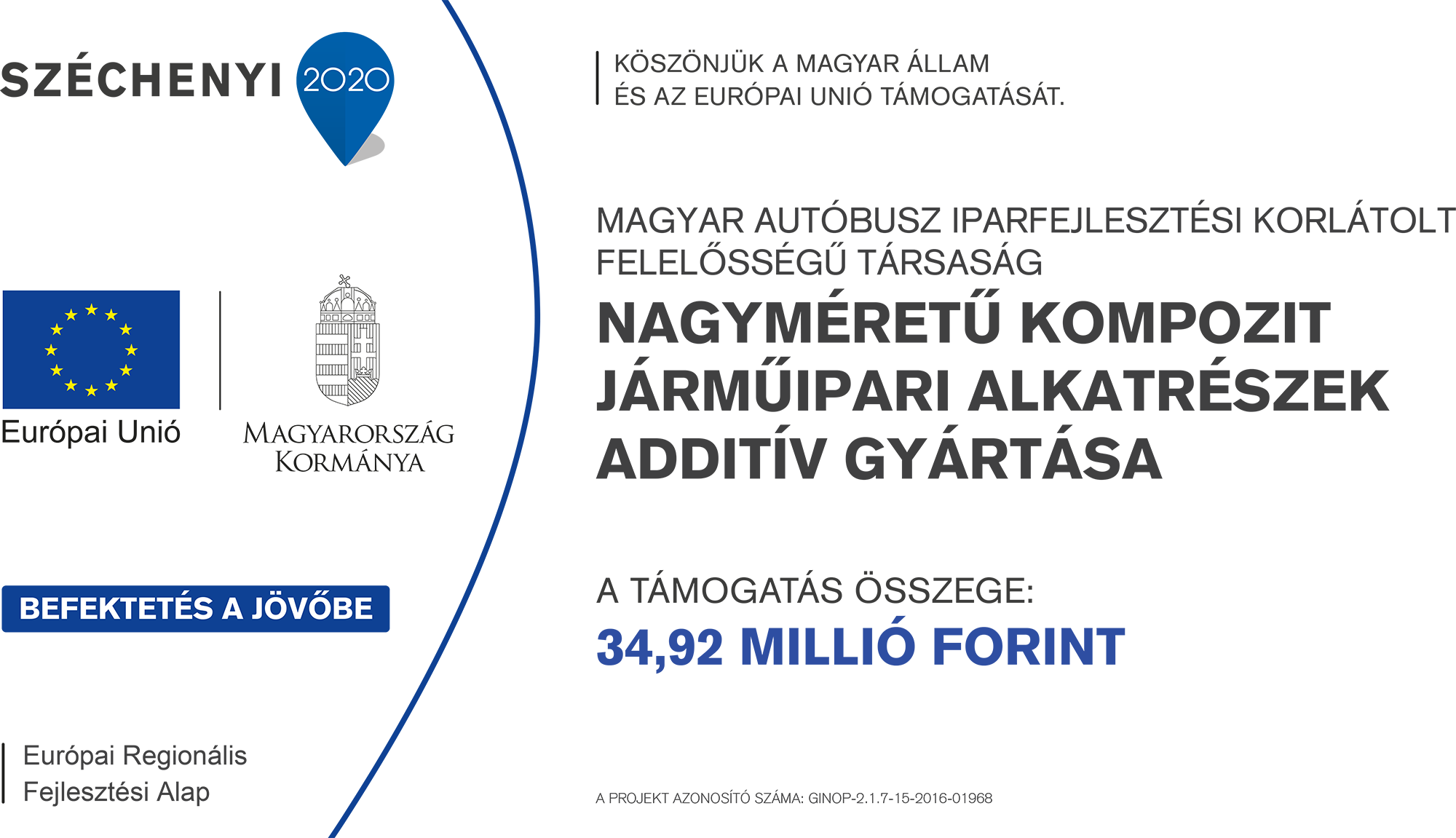